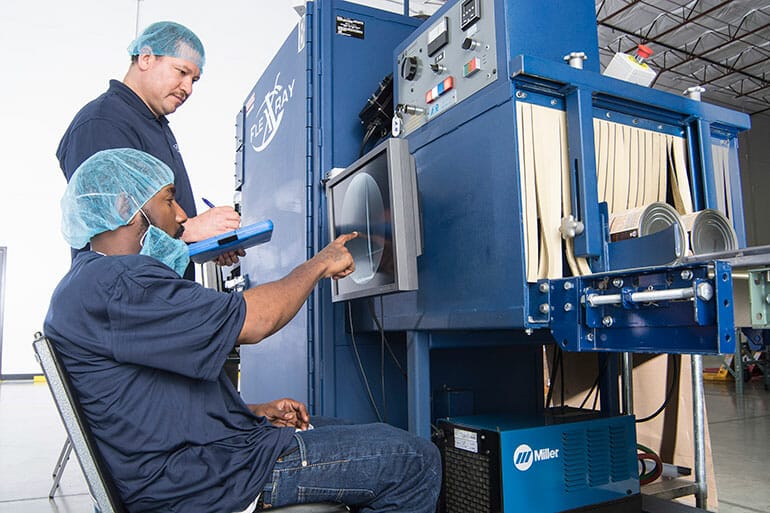
Ensuring food safety is critical for every food producer. Physical contamination—when foreign objects enter the food supply—poses serious risks to consumers and your brand’s reputation. This guide explores how to detect and prevent physical contamination in food production, with actionable tips and cutting-edge solutions to safeguard your operations.
What Is a Physical Contaminant in Food?
Physical contaminants are unintended objects or materials that can enter food during any stage of production or packaging. Common examples include:
- Metal fragments from machinery
- Glass shards from broken containers
- Plastic pieces from equipment or packaging
- Wood splinters from pallets or crates
- Natural debris such as stones, shells, or bones
These contaminants can harm consumers and lead to costly recalls. Identifying and preventing physical contamination is essential to maintaining food safety standards.
How Can You Detect If Food Is Contaminated?
Detecting physical contamination in food requires advanced technology and robust quality control systems. Common methods include:
Visual Inspections: Trained employees visually check for contaminants during production. While simple, this method is not foolproof.
Metal Detectors: These can find metal fragments in packaged or bulk foods. However, they are limited to metallic contaminants.
X-Ray Inspection Systems: Advanced X-ray technology, like that offered by FlexXray, can detect a wide range of contaminants, including glass, plastic, and bone. This method is highly effective for ensuring product safety.
Magnetic Separators: Available in an array of designs and suitable for a variety of uses, modern-day bar, plate, grate, trap, and suspended magnets find and remove fine, high-purity metal contaminants during food processing.
FlexXray specializes in identifying and resolving contamination issues with unparalleled precision. Our X-ray inspection services can identify even the smallest contaminants, ensuring your products meet the highest safety standards.
How to Prevent Physical Contamination in Food Production
Preventing physical contamination requires a proactive approach. Here are key strategies to implement:
Regular Equipment Maintenance
Conduct routine inspections and maintenance of all machinery to prevent wear and tear that can lead to metal or plastic fragments entering the food supply.
Employee Training
Educate employees about the importance of food safety and proper handling procedures to minimize contamination risks.
Quality Control Protocols
Establish robust quality control measures, including random product checks and thorough documentation of safety practices.
Advanced Detection Technology
Invest in detection systems like X-ray inspection to identify contaminants early and avoid widespread issues.
Supplier Audits
Work closely with suppliers to ensure raw materials meet safety standards and are free from contaminants.
Common Sources of Food Contaminants
Understanding the root causes of physical contamination can help producers address vulnerabilities in their processes. Key sources include:
- Raw Material Handling: Natural debris or foreign objects can enter the supply chain at the raw material stage.
- Production Processes: Machinery or equipment malfunctions can introduce contaminants.
- Packaging: Damaged or defective packaging materials can contaminate food.
- Storage and Transportation: Poor handling practices during storage or shipping can result in contamination.
By identifying these risks, producers can take targeted actions to reduce contamination incidents.
Why Choose FlexXray for Contamination Detection?
FlexXray is the trusted partner for food producers seeking to detect and resolve physical contamination issues. Here’s why:
Precision Technology: Our X-ray inspection systems can detect contaminants as small as 0.8 mm.
Fast Turnaround: We prioritize quick results to minimize downtime and keep your production running smoothly.
Unmatched Expertise: With decades of experience, we understand the unique challenges food producers face.
Partner with FlexXray to ensure your products meet the highest safety standards and protect your brand’s reputation.
Other Frequently Asked Questions
A physical contaminant is any foreign object that accidentally enters food during production, such as metal, glass, plastic, or natural debris.
Advanced technologies like X-ray inspection systems are the most reliable way to detect physical contaminants in food.
Prevent contamination by implementing robust quality control measures, regular equipment maintenance, employee training, and investing in detection technology like FlexXray’s services.
Contaminants can include physical objects, chemical substances, or biological agents that compromise food safety. Physical contaminants are among the most common challenges for producers.
Take Action to Protect Your Products
Physical contamination can threaten consumer safety and your brand’s reputation. Don’t take chances with your food production process. Contact FlexXray today to learn how our advanced X-ray inspection services can help you detect and prevent physical contamination effectively.
Leave a Reply
You must be logged in to post a comment.